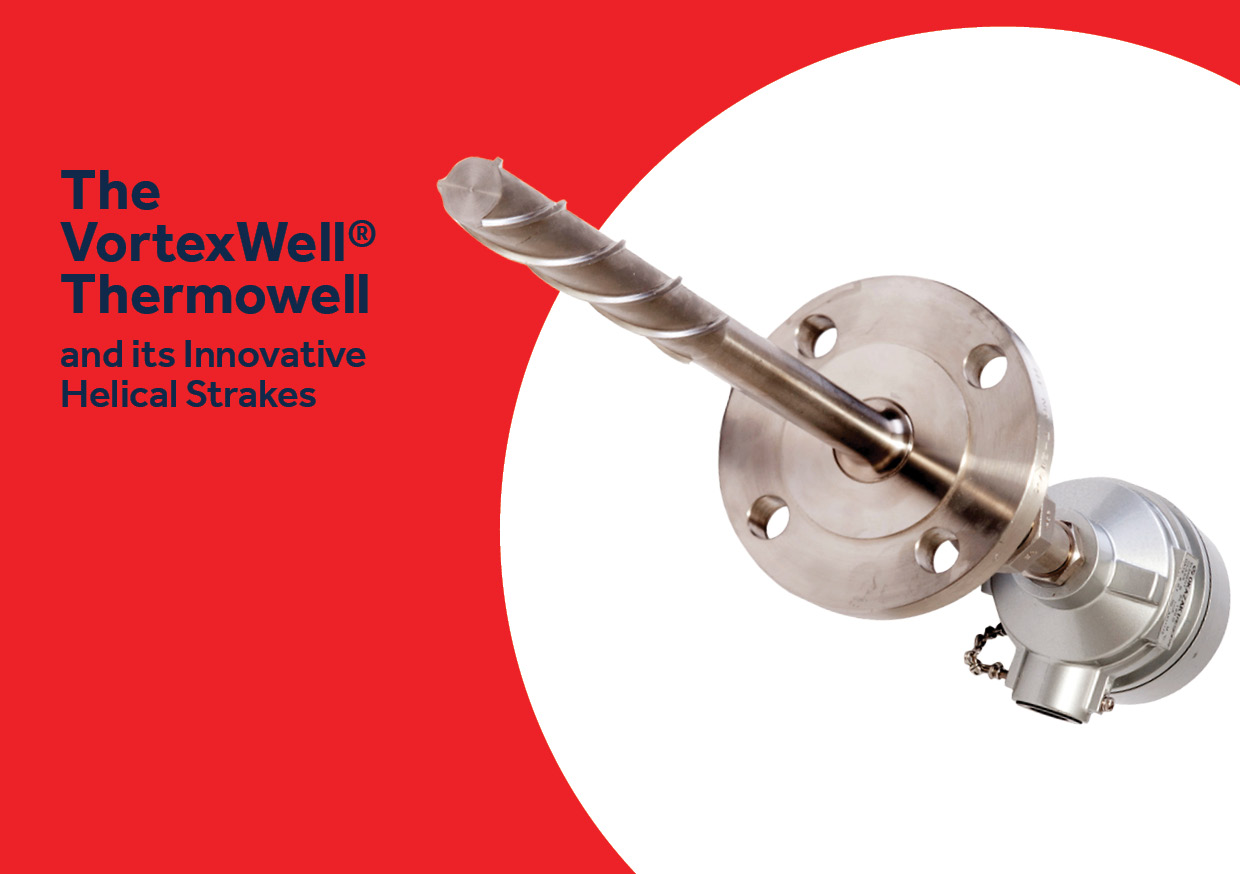
The VortexWell® and its Innovative Helical Strakes
At Okazaki we are very proud of our VortexWell® Thermowell. So I thought it would be good to discuss the Helical Strake design we have used and how it works to greatly reduce the formation of Vortices.
Why the VortexWell®?
When fluid flows around a blunt object in it’s path, such as a standard Thermowell, it forms vortices downstream of the object. This is commonly known as Vibration Induced Vortices. The implications of these vortices can have a huge impact, from inaccurate readings to complete failure of the thermowell.
After extensive R&D and independent evaluation, we have developed a unique design of thermowell which we call the VortexWell®. This doesn’t require a velocity collar and is cost effective for the end user in terms of purchase, installation and maintenance costs.
What is the VortexWell®?
The VortexWell® incorporates an innovative helical strake design, very similar to the helical strakes seen on columns and cooling towers. By using the latest CFD software to visualize the flow behaviour, we were able to accurately compare a standard tapered thermowell and the VortexWell®.
In the tests, the standard tapered thermowell showed classic shedding behaviour as expected, whereas the VortexWell® demonstrated no signs of natural flow behaviour. The VortexWell® helical strake design disturbed the flow sufficiently to interrupt the regular formation of vortices. Whilst a small vortex was observed in the wake of the VortexWell® this was a localized stagnation point and didn’t shed.
How the VortexWell® works?
As the vortex shedding frequency approaches the thermowell natural frequency, the tip displacement and stresses are greatly magnified and the thermowell can fail. Even when the thermowell has passed calculations to the ASME PTC 19.3 standard, failures are still known to have happened, Monju Power Plant being a prime example.
To solve this issue, we looked at several different ideas, from increasing damping to streamlined cross sections. It was found that the best solution was to incorporate a helical strake as a vortex suppression method which made our VortexWell the best performing and safest thermowell available.
More information.
If you’d like to learn more about our VortexWell® Thermowell you can view more information here https://www.okazaki-mfg.co.uk/products/sensors/vortexwell-thermowell.
Alternatively, you can all us on 029 2081 4333 or email the team on sales@okazaki-mfg.co.uk.